Extrusion of Silicone Rubber
Providing high-quality and customized solutions for extrusion of silicone rubber. Your trusted partner for precise and efficient silicone rubber manufacturing services.
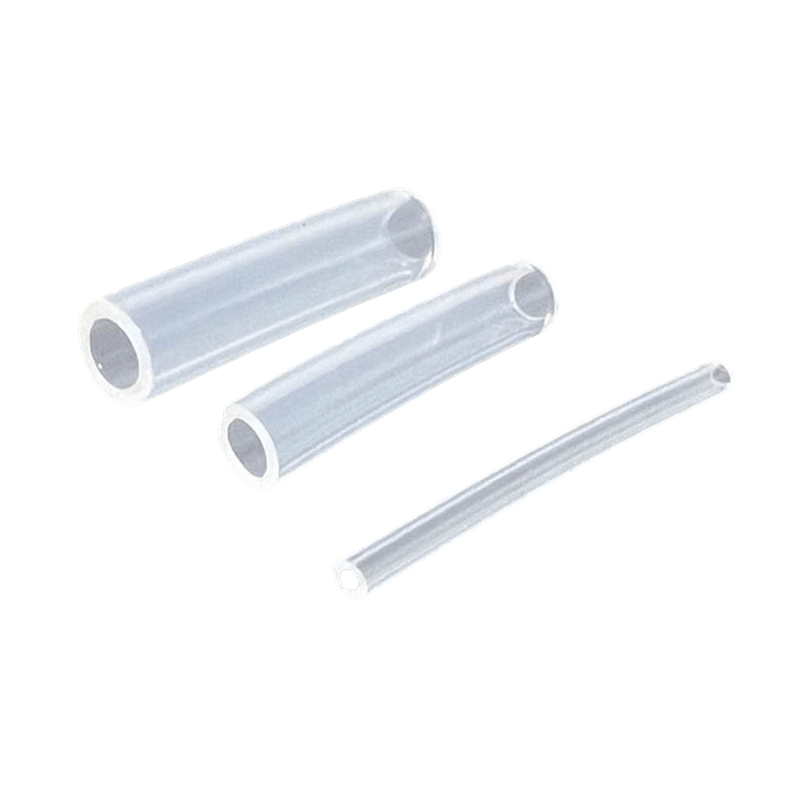
Custom Silicone Rubber Extrusion Service
With our extensive experience in producing extruded silicone and rubber products, we possess the expertise to formulate custom compounds that are tailored specifically to meet the unique design and application requirements. This allows us to achieve precise engineered performance while optimizing costs. Our capabilities extend to handling custom components ranging from simple to extraordinarily complex, ensuring that we can fulfill even the most intricate project demands.
Why Choose Us for Silicone Rubber Extrusion Service?
Expertise in the Process
With over 20 years of experience and specialized knowledge in extrusion manufacturing, our team is well-versed in every aspect of the silicone and rubber extrusion process. From material selection to die design and control of extrusion parameters, we ensure product quality and consistency.
Customization Capability
We have the ability to customize the manufacturing of silicone and rubber extruded components according to specific customer requirements and design needs. Our engineering team works closely with customers, providing technical consultation and design support to ensure the final product meets their expectations.
Material Selection and Formulation Optimization
We offer a wide range of silicone and rubber material choices and can optimize formulations to meet specific physical performance requirements based on customer's application needs. Our team of experts conducts material selection and testing to ensure the performance and reliability of the extruded components.
Capability to Handle Complex Shapes
We have the ability to handle a variety of complex shapes, whether it's intricate cross-sectional designs, detailed features, or extruded components with special requirements. Our technical team and process engineers are adept at addressing the challenges posed by complex shapes and ensuring the manufacture of extruded components that meet design specifications.
Manufacturing Precision
By tightly controlling parameters such as temperature, pressure, and speed during the extrusion process, we can produce silicone and rubber extruded components with precise dimensions and consistency. We employ advanced equipment and monitoring systems to ensure product quality and manufacturing precision.
Quality Control and Certifications
We strictly adhere to quality control standards and processes to ensure that each extruded component meets industry standards and customer requirements. Our manufacturing processes comply with ISO quality management systems, and we can provide relevant certification documents and test reports.
Our Unique Points
An extensive range of customizable options, seamless collaboration for tailored solutions, and swift manufacturing to capitalize on market opportunities and meet urgent demands
Endless Options
Choose from millions of possible combinations of materials, finishes, tolerances, markings, and certifications for your order.
Seamless Customization
We collaborate closely with you to bring your vision to life. With a wide array of materials, colors, and finishes, your creative ideas take shape with precision and unmatched quality.
Shorter Delivery Times
We can start manufacturing immediately according to your needs, achieving rapid delivery, enabling you to seize the market opportunities and meet urgent customer demands.
Start Making Custom Silicone Rubber Extrusion Components
Looking for precision and customization in silicone rubber extrusion molding? Contact us today for expert solutions tailored to your unique needs!
Lingshan Tech’s Multi-material Assembly Solutions
Available Materials for Silicone Rubber Extrusion Parts
Silicone Rubber
FDA-Grade Silicone
High-Temperature Silicone
Electrically Conductive Silicone
Ethylene Propylene Diene Monomer
EPDM70
EPDM75
EPDM80
Neoprene Rubber
CR 232
CR 435
Nitrile Rubber, NBR
NBR70
NBR80
NBR90
Viton®
Viton® A
Viton® B
Viton® G
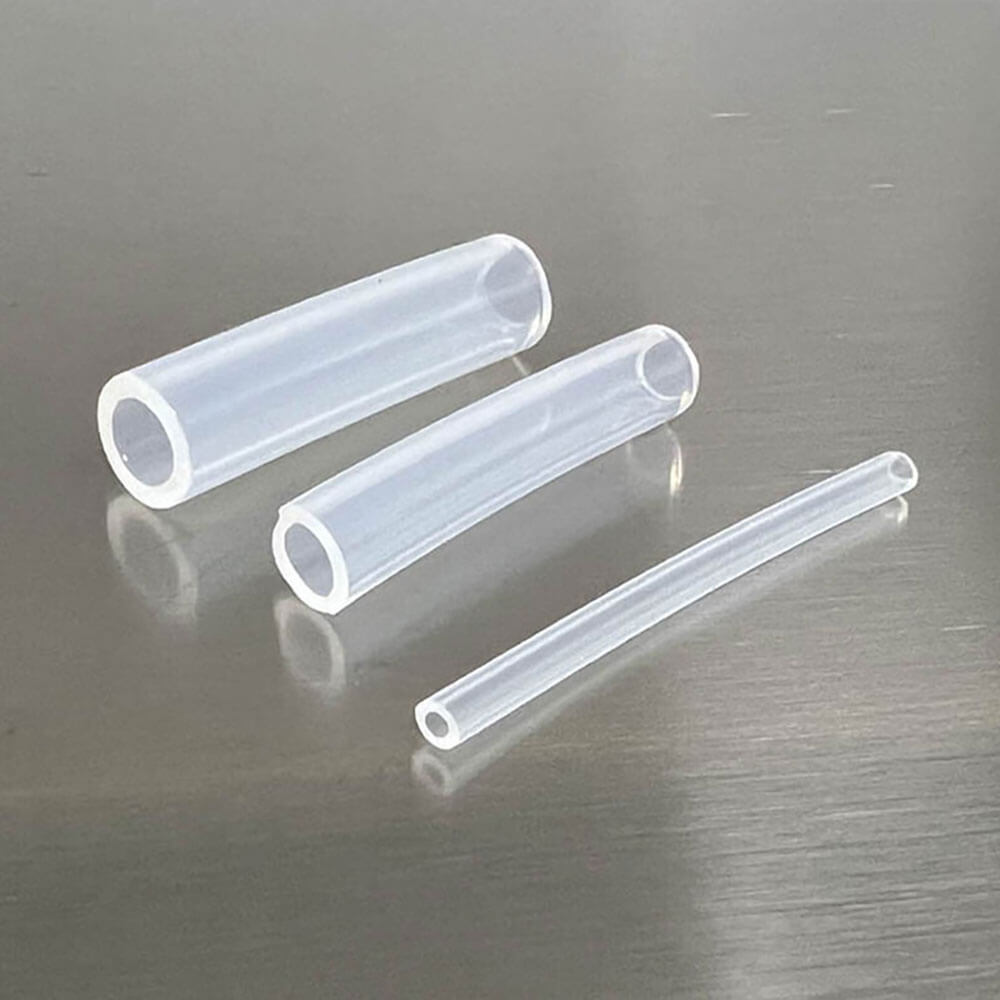
Tolerance of Silicone Rubber Extrusion Parts
The tolerance for silicone rubber extrusion parts can vary depending on the specific requirements of the application, the complexity of the part, and the capabilities of the manufacturing process.Here are some general guidelines for tolerance considerations in silicone rubber extrusion parts:
Standard Tolerances
Silicone rubber extrusion processes typically allow for relatively tight tolerances, often measured in thousandths of an inch (or millimeters). The specific tolerances will depend on the manufacturer's capabilities and the complexity of the part.
Material Characteristics
The type of silicone rubber used can impact tolerance. Some silicone formulations are more elastic and may have slightly larger tolerances, while others are more rigid and can achieve tighter tolerances
Customer Requirements
Tolerance requirements can vary from one customer or application to another. It's essential to communicate specific tolerance needs with your extrusion manufacturer.
Testing and Verification
Testing and verification processes may be used to confirm that parts meet tolerance specifications. This can include measurements using specialized equipment.
Geometry Complexity
The complexity of the part's geometry can influence the achievable tolerances. Simple, straight extrusions may have tighter tolerances compared to parts with intricate cross-sectional designs or complex features.
Quality Control
Manufacturers may employ quality control measures to ensure that parts meet specified tolerances. This can include inspection and measurement during and after the extrusion process.
Industry Standards
In some industries, such as aerospace or medical devices, there may be industry-specific standards that dictate tolerance requirements for silicone rubber extrusion parts.
Design Considerations
Design engineers should work closely with the extrusion manufacturer to ensure that the design allows for achievable tolerances within the capabilities of the extrusion process.
Some Common Surface Finish Options for Silicone Rubber Extrusion Parts
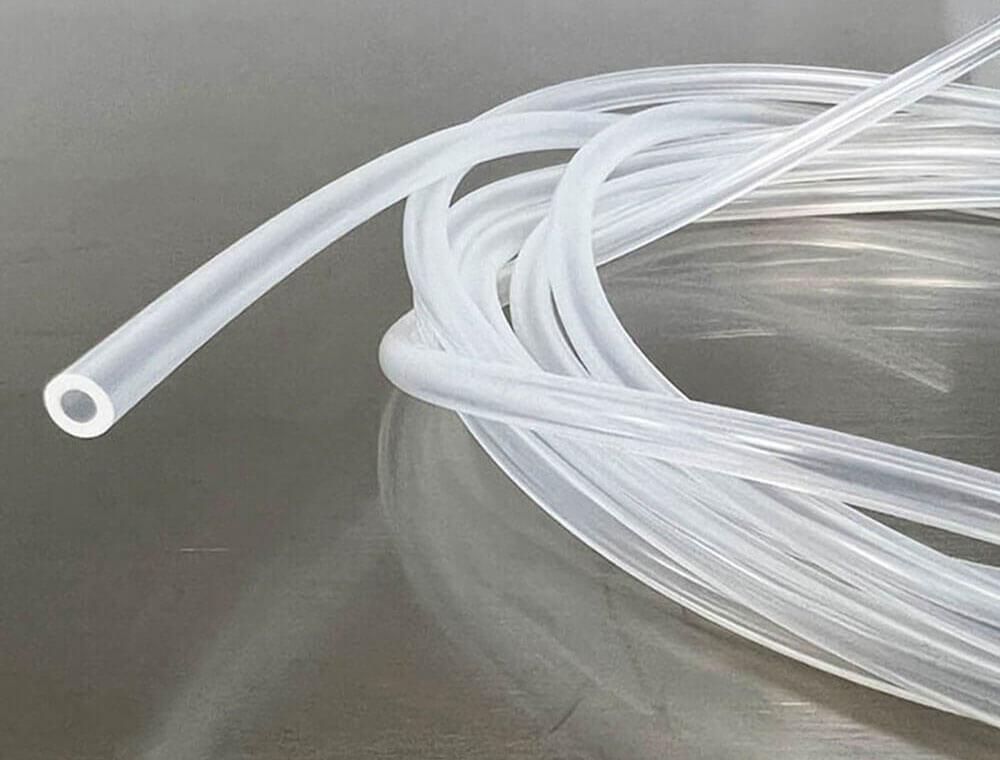
Surface Finish Options:
- Natural Surface
- Polishing
- Matte Finish
- Coatings
- Color Dyeing
- Texture or Pattern Embossing
- Silicone Coating
- Cleaning and Decontamination
What Is Silicone Rubber Extrusion?
Silicone rubber extrusion is a manufacturing process used to create custom shapes, profiles, and components made from silicone rubber. It involves forcing a silicone rubber compound through a specially designed die or extrusion tool to create continuous lengths of the desired shape or cross-section. This process is commonly used in various industries to produce a wide range of silicone rubber products with specific characteristics and dimensions.
The Key Steps Involved in Silicone Rubber Extrusion:
Material Preparation
Extrusion
Cooling and Curing
Cutting and Finishing
The Advantages of Silicone Rubber Extrusion:
Customization
High Precision
Complex Shape Handling
Wide Applicability
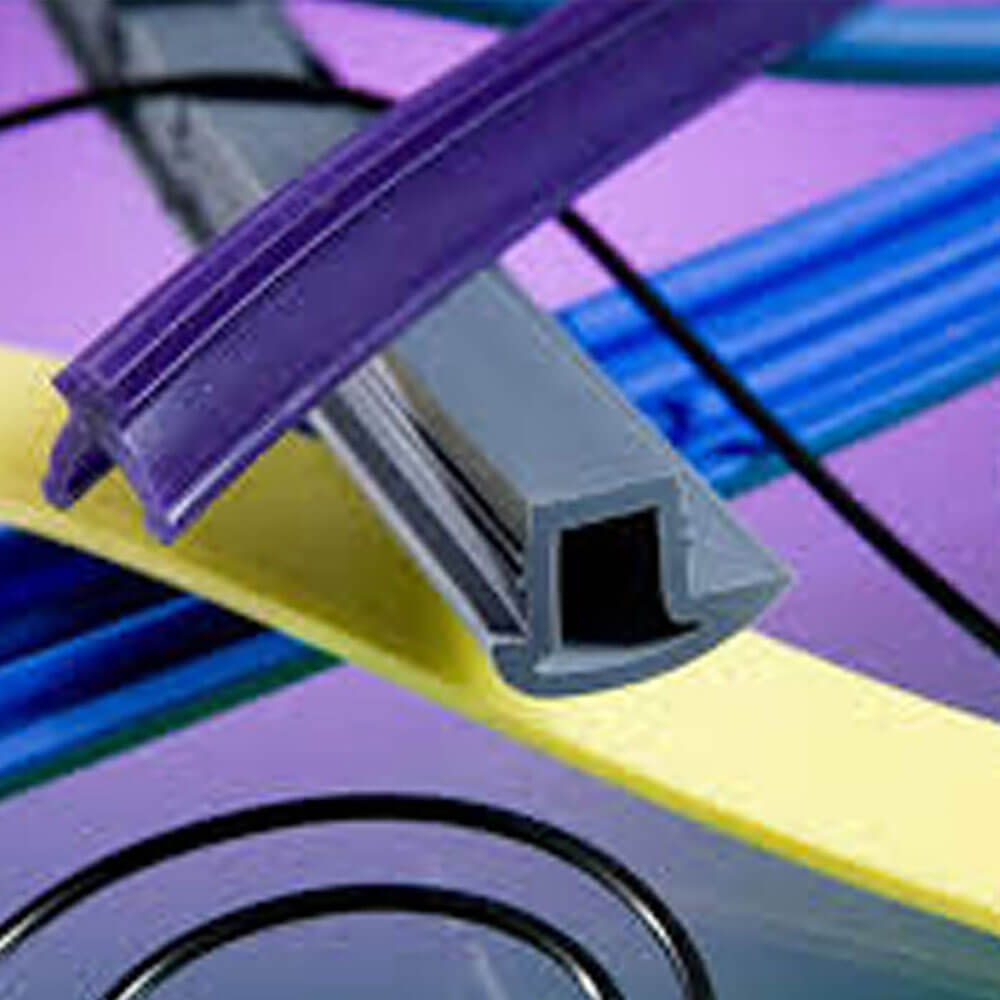
Applications of Silicone Rubber Extrusion
- Typical Applications of Extruded Silicone Profiles
- Automotive – Seals & Gaskets
- Aerospace and military Seals & Gaskets
- Meat Processing – Hatch Seal, Chamber Seals
- Lighting Industries
- Construction -(door seals, window seals, protective seals between glass & steels)
- Dairy Fluid Handling Tubing and Dairy Seals
- Electronics washers, spacers and seals
- Door Seals & Gaskets
- Oven and manway seals
- High temperature sealing
- HVAC Equipment – wire seals, sealing chambers conditioning
- Rail and Mass Transit Seals
- Oil & Gas resistant seals
- Pharmaceutical USP Class Vi Tubing and Custom Seals
- Marine and Defense – Hatch Seal, Inflatable Seals, Molded Rubber Parts