What We Do?
Lingshantech excels in producing medical devices using silicone, plastic, and metal stamping components. We focus on empowering customers through partnerships to enhance efficiency, reduce costs, comply with regulations, drive innovation, and achieve business success.
As a contract manufacturer in the medical device industry, we specialize in silicone and plastic materials, providing breathing masks, anesthetic masks, and hearing aid components. Our LSR and plastic manufacturing capabilities enable us to produce the latest medical devices and components with the highest quality assurance.
ISO-certified Class 8 Cleanroom
Our ISO-certified Class 8 cleanroom includes LSR and plastic molding machines, ensures a highly clean manufacturing environment for components, ensuring that products meet the hygiene and quality standards of the medical industry. This provides reliable manufacturing assurance for your products.
Material Diversity
We offer a variety of materials such as plastic, silicone and metal, which can meet the specific requirements of different products. From durable metal parts to soft silicone accessories, you can choose the most suitable material for your needs to ensure excellent product performance.
Advanced Manufacturing Technologies
Utilizing plastic and silicone (including LSR) molding, 3D printing, CNC machining, metal stamping and more, we manufacture complex and precise medical components. From medical silicone face masks to delicate LSR hearing aid accessories, precision surgical instrument components, and complex medical assist device structures. We have customized solutions for all of them!
Quality Control
Our manufacturing strictly adheres to ISO certified standards, from selecting quality materials to comprehensive final-stage quality assessment. Meticulous attention to detail ensures unwavering product quality and compliance. We deliver medical components with exceptional precision, reliability, and compliance. Our state-of-the-art Class 8 clean room environment guarantees optimal conditions for medical product manufacturing.
Industry Certifications
- ISO 9001
- ISO 13485
- IATF16949
- Medical-grade, FDA-approved
Comprehensive Quality Documentation
- CMM Inspection Report
- First Article Inspections (FAI)
- Full Dimensional Inspections
- Material Test Reports (TDS)
- Material Certificates
- Certificates of Conformance
Far-reaching Capabilities
- CNC machining (including 3-axis and 5-axis), milling & turning
- Injection molding of silicone and plastic
- FDM and SLA 3D printing
- Multiple metals & plastics
- Functional & cosmetic post-processing options
More Services We Provide
- Tooling export
- Parts assembly
- After-sales support
- Supply chain management
- Testing and quality control
- Logistics and shipping
- Component sourcing and procurement
Why Choose Lingshantech for Medical Industry?
We specialize in reliable medical device prototyping and production, handling simple to complex medical parts. Our advanced technologies and manufacturing expertise bring your medical products to life efficiently. Whether it's rapid prototyping, bridge tooling, or low-volume production, we help you achieve your goals.
Strong Capabilities
Lingshantech ensures the highest manufacturing capabilities, material certifications, and advanced technologies, providing medical device components that meet all regulatory compliance requirements
Precision Parts
Our medical device prototyping services provide parts meeting tight tolerance and precision requirements, manufacturing medical components with tolerances up to +/-0.05mm
Fully Customizable
Lingshantech accelerates medical parts manufacturing through custom design and tooling capabilities, analyzing product uniqueness and utilizing high-tech manufacturing processes to bring concepts to life.
Instant Quotation
Our ever-learning instant quotation platform improves the medical parts manufacturing experience, offering DFM, pricing, and lead time, also tooling 3D design files, along with efficient order tracking and management capabilities.
Optimizing Projects for Medical Devices
Tool & Mold Building
A successful part starts with a well-designed mold.Our Tool & Mold Building expertise brings precision and efficiency to the production of medical device components.
Design for Manufacturability
DFM (Design for Manufacturing) is crucial for optimizing designs and streamlining production. Our DFM expertise enhances medical device component manufacturing by ensuring efficient production processes and high-quality results.
Materials Selection
Material selection is pivotal for product performance. Our extensive expertise in material selection enriches medical device components by ensuring the right materials for durability, safety, and functionality.
Metrology
Metrology ensures precision and quality, aligning seamlessly with our manufacturing expertise to guarantee accuracy in all aspects.
Material for Medical Devices
- Thermoplastics: (ABS, PC, PE,PP, PVC, PS, PMMA)
- Thermosets: (PA, PI, PUR, EVOH)
- Metals: (Stainless Steel,Titanium Alloy,Aluminum,Nickel Titanium Alloy,Iron,Copper,Alloys)
- Nylon
- Silicone&LSR
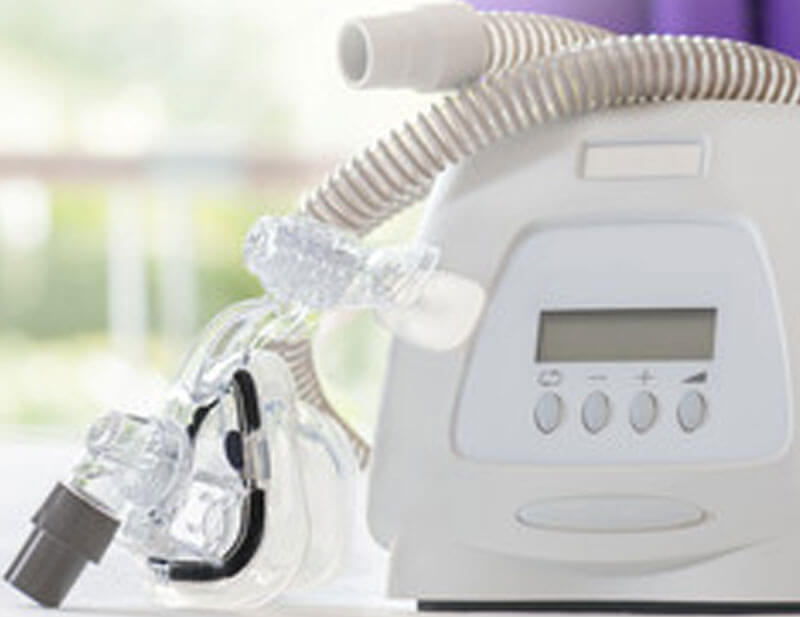
Plastic Medical Components
Plastics' versatility, cost-effectiveness, biocompatibility and ability to be molded into complex shapes while being compatible with sterilization processes make them ideal for the manufacture of medical products that require precision and reliability.
We offer a wide range of plastics solutions for the medical industry, whether it's for medical devices, components or packaging, covering everything from small parts to complex instrument components and their packaging.
Liquid Silicone Rubber(LSR)Medical Components
Medical-grade liquid silicone rubber (LSR) in conjunction with Lingshantech's advanced molding technology, ISO Class 8 clean room facilities, and highly automated LSR/LSR 2-shot/multi-shot manufacturing processes provides a multitude of benefits. These encompass improved clarity, heightened chemical resistance, unparalleled purity, for the fabrication of intricate high-precision silicone components,including but not limited to catheters, seals, gaskets, respiratory masks, surgical instruments and wearable medical devices.
Plastic:
- Disposable medical plastic equipment (plastic infusion devices, injection syringes, blood transfusion tubes, extension tubes, connection tubes, and drainage bags)
- Plastic human organs and surgical aids (catheters, laryngeal masks, artificial kidneys, artificial lungs, and artificial joints)
- Medical plastic parts (PVC face masks, medical plastic tubing, tracheal intubation devices, tracheal tubes, endovascular intubation tools)
- Medical plastic packaging materials (eye drop medicine bottles, oral liquid bottles, PVC plastic bottles, and low-density polyethylene ointment tubes)
- Medical plastic containers (bedpans, wash basins, and packing bags)
- Clinical plastic products and consumables(test tubes, centrifuge tubes, petri dishes, measuring cups, and more)
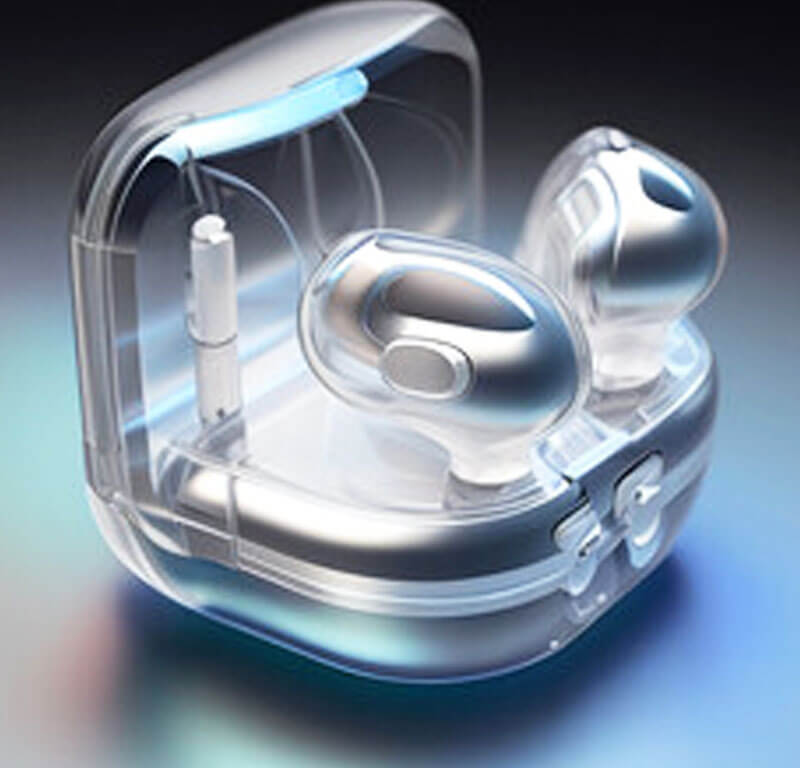
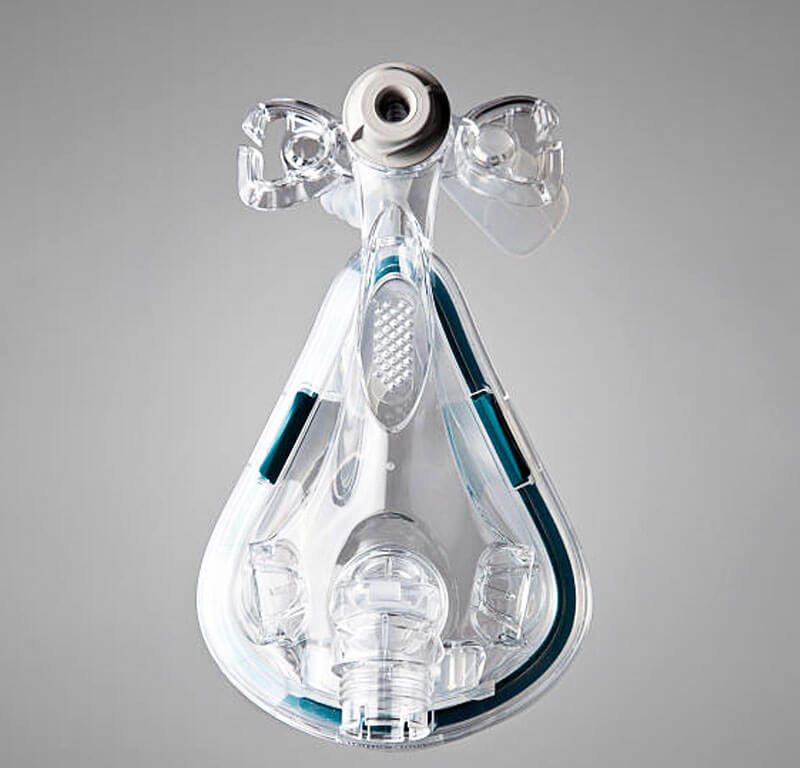
Silicone & LSR:
- Medical device seals (O-rings for surgical tools, syringes, and infusion devices)
- Biocompatible implants (soft tissue fillers, and nasal prosthetics)
- Waterproof protection components
- Medical-grade tubing ( urinary catheters, endotracheal tubes, and vascular catheters)
- Surgical instruments ( scalpel handles, surgical tool grips)
- Medical protective equipment ( face masks, eye shields) tubes, centrifuge tubes, petri dishes, measuring cups, and more
Metal:
- Steel Blades and Handles
- Titanium Alloy Bone Screws and Plates
- Aluminum Alloy Handles and Operating Parts
- Metal Springs and Clamps
- Stainless Steel Wires and Electrodes
- Cobalt-Chromium Alloy Stents
- Copper Alloy Electronic Connectors
- Aluminum Alloy Casings and Frames
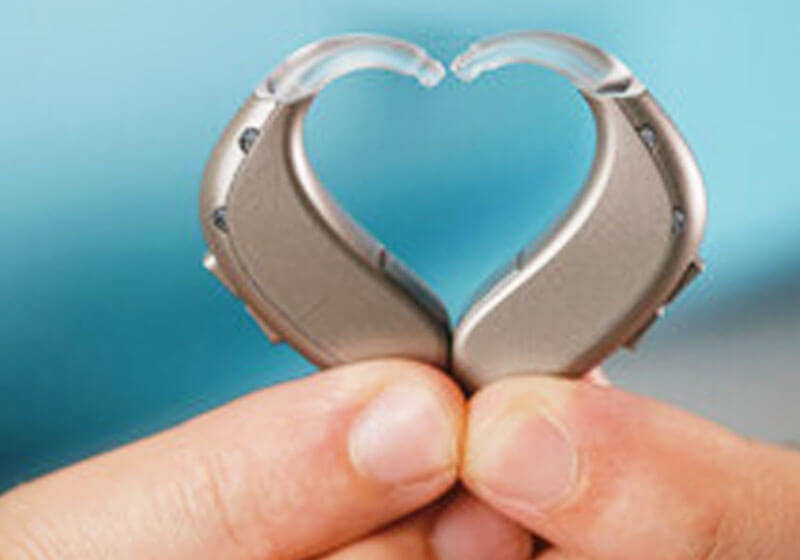