Custom Die Casting Service
We offer high-output production capacity, low cost, and flexible part design options making it an appealing casting choice for non-ferrous metal products. Our die casting facilities are equipped to handle a variety of designs, materials, and manufacturing needs across multiple industries.
Hot Chamber & Cold Chamber Die Casting
Tool Manufacturing in Up to Days
ISO9001:2015
IATF16949
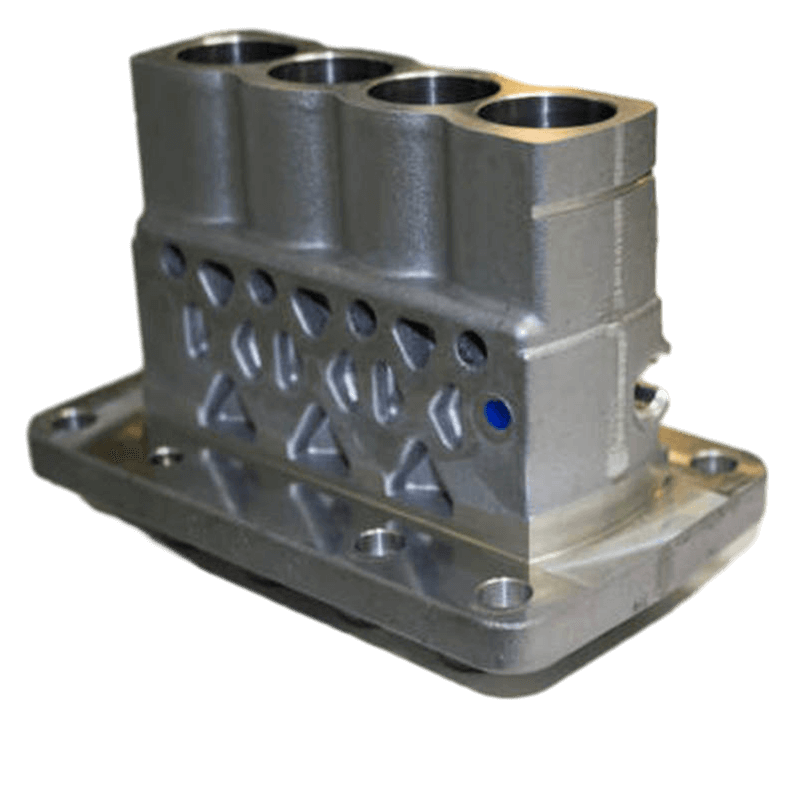
Our Precision Die Casting Services
Lingshantech boasts advanced die casting equipment and cutting-edge technology, enabling us to leverage our expertise in producing parts with intricate geometries, tight tolerances, and robust mechanical properties. This capability allows us to deliver high-quality, on-demand parts to meet the diverse needs of various industries.
Why Choose Lingshantech's Die Casting Services?
Extensive Selections
we ensure efficient and fast production of your casting parts. Our state-of-the-art automated facilities enable us to handle a variety of complex customized die casting projects with ease.
In House Plant & Facilities
we ensure efficient and fast production of your casting parts. Our state-of-the-art automated facilities enable us to handle a variety of complex customized die casting projects with ease.
Endless Options
Explore countless possibilities with millions of combinations for materials, finishes, tolerances, markings, and certifications for your order.
Strict Quality Control
As an ISO 9001:2015 and IATF16949 certified company, we are dedicated to delivering precision die casting services. Our engineering team at Lingshantech conducts thorough quality inspections at various stages of the manufacturing process, including pre-production, in-production, first article inspection, and before delivery, ensuring the production of the highest quality parts.
In-House Design and Finishing Services
In addition to high pressure die casting, we offer early design engineering development and prototype services as well as complete in-house secondary solutions including machining, finishing and assembly.
Full Range of Services
We provide a full range of services outside of the primary operation of die casting parts. Our secondary in-house operations include painting, CNC machining, stamping, injection molding, welding and more.
Our Unique Points
Die casting is a highly efficient method for producing high-quality prototypes and small-batch parts, making it a versatile choice for various applications. Our team is dedicated to helping you achieve your manufacturing goals by offering expert die casting services
Rapid Prototyping
We possess the ability to swiftly and flexibly generate high-quality prototypes, regardless of material diversity or design modifications. Our manufacturing process upholds a high level of precision and consistency, guaranteeing the provision of outstanding prototypes that serve as robust aids for testing and validating design concepts.
DVT & PVT Testing
We specialize in creating die casting products ideal for market and consumer testing, concept models, and user evaluation during the Design Validation Testing (DVT) and Production Validation Testing (PVT) stages. Our die casting services enable you to swiftly incorporate changes for thorough performance and dimensional testing before market launch.
Pilot & Mass Production
Die cast parts are excellent for custom and first-run production, allowing cost-effective product quality testing before proceeding to full-scale manufacturing. We offer small batch and large-scale production services, accompanied by PPAP (Production Part Approval Process) documentation for quality assurance and validation.
Start A Die Casting Project Today
Whether your project requires complex shapes, multiple components, high dimensional accuracy, or corrosion resistance, we are available to provide assistance. To learn more about our custom die casting processes or to receive a quote for your project.
Available Materials for Metal Stamping
Aluminium Alloys
Aluminium 46100 / ADC12 / A383 / Al-Si11Cu3
Aluminium 46500 / A380 / Al-Si8Cu3
Zinc Alloys
Zamak 2
Zamak 3
Zamak 4
Zamak 5
Zamak 7
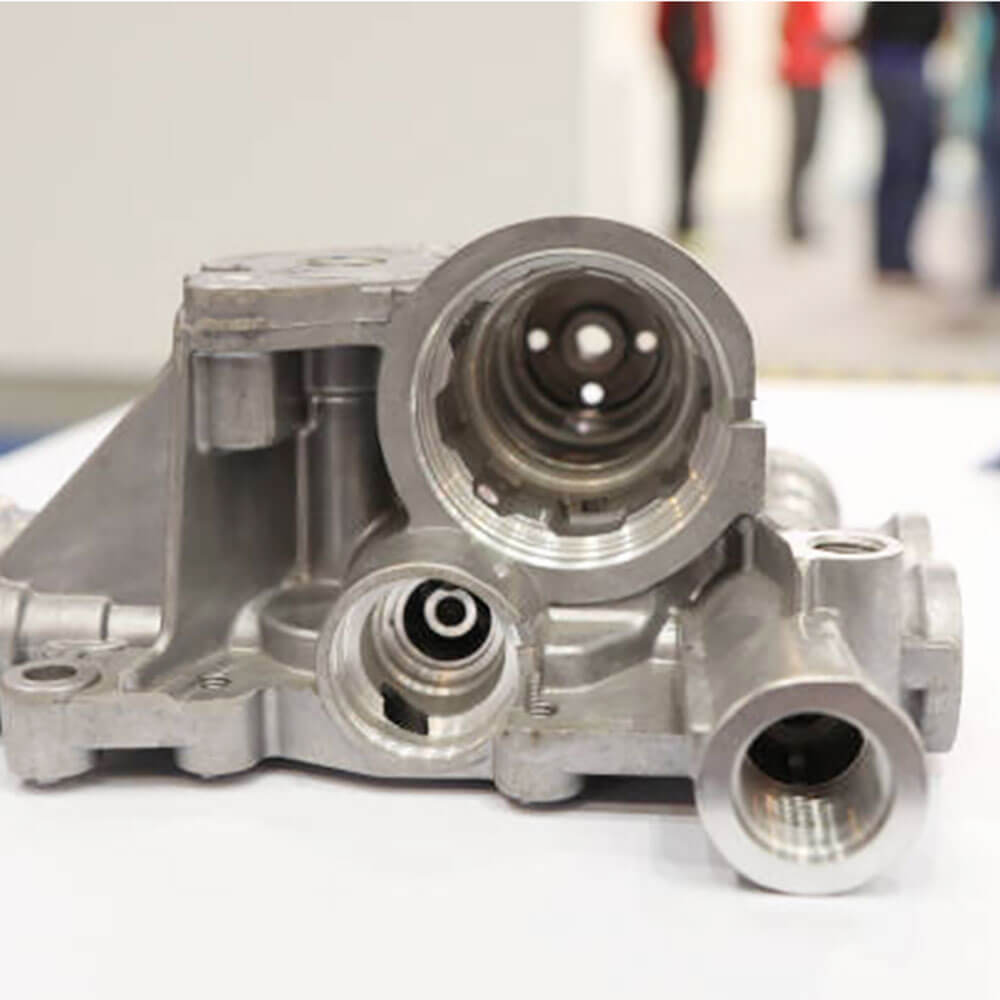
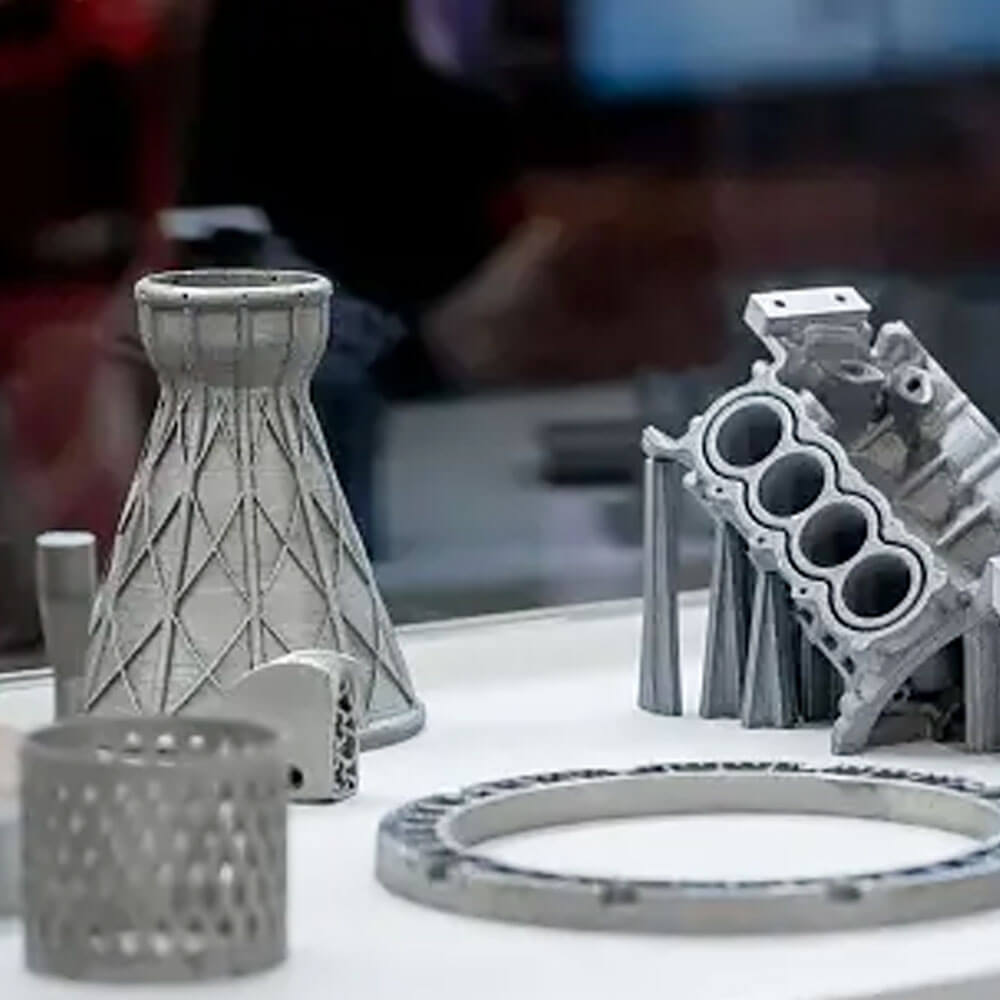
Tolerances
Our die casting service is characterized by extremely high precision, with tolerance control achievable within ±0.004 inches (0.1 millimeters). This high level of accuracy ensures the production of consistently high-quality parts, whether in the prototype development phase or during mass production. Such precision is particularly critical for industries requiring highly precise components, such as aerospace, medical equipment, and electronics.
Surface Finishes for Die Casting
Post-processing and finishing is the final step of precision die casting. Finishing can be applied to remove the surface defects of cast parts, enhance mechanical or chemical properties, and improve products’ cosmetic appearance. There are some types of die casting surface finish options.

Common 3D Printing Applications
Available Die Casting Finishes
Standard (As-Cast)
Bead Blasted
Anodized (Type ll Or Type Ill)
Powder Coating
Wet Painting
Plating
Chemical Film
Media Tumbled
Custom
What Is Die Casting?
Die casting is a highly efficient and precise manufacturing process used to produce metal parts and components. In this process, molten metal is forced into a mold cavity under high pressure, where it solidifies and takes on the shape of the mold. Once the metal has cooled and solidified, the mold is opened, and the finished part is removed.
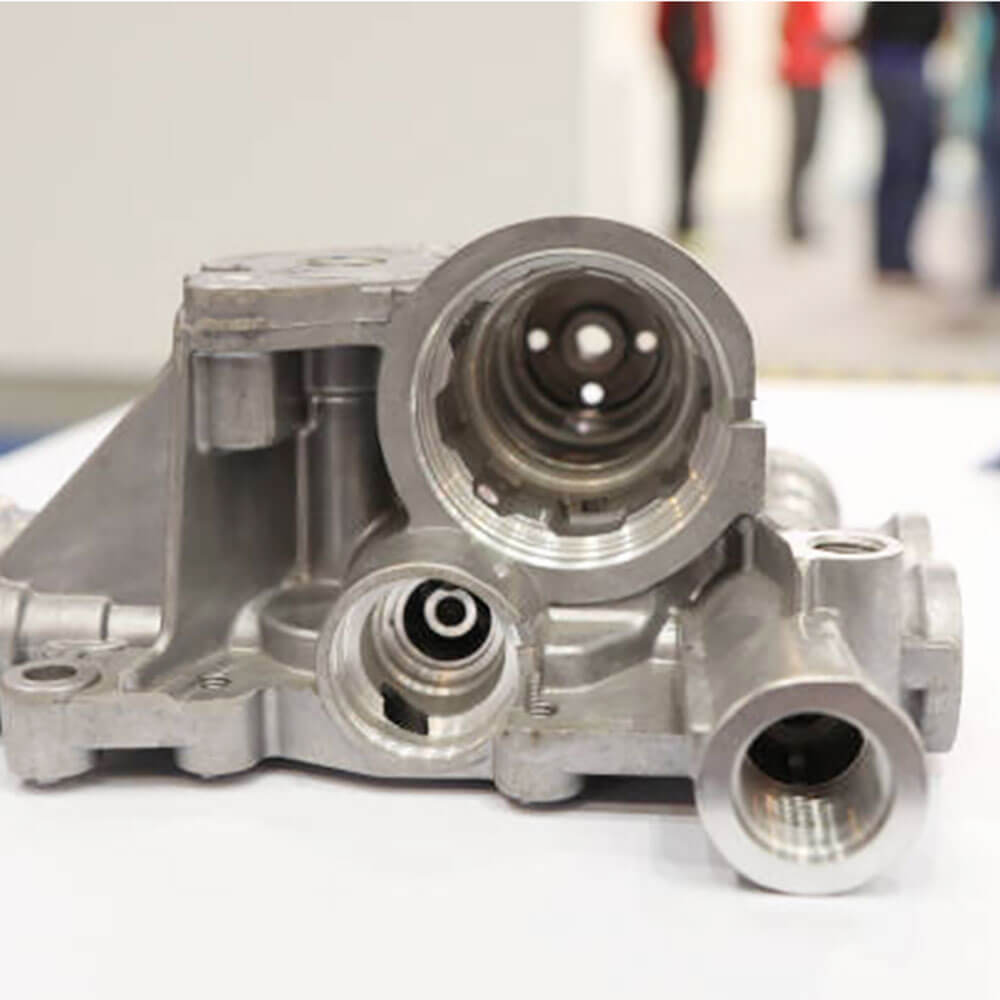
There Are Two Primary Types of Die Casting:
- Hot Chamber Die Casting: In this method, the metal is melted in a furnace and then transported to the die casting machine through a gooseneck or ladle. This process is typically used for metals with lower melting points, such as zinc and magnesium.
- Cold Chamber Die Casting: This process is used for metals with higher melting points, such as aluminum and copper. In cold chamber die casting, the molten metal is ladled into a chamber, and a hydraulic piston forces the metal into the mold cavity.
Die Casting Offers Several Key Advantages Such As:
- High Precision
- Efficient Production
- Consistency
- Smooth Surface Finish
- Material Variety
- Cost-Effective
- Strength and Durability
- Complex Geometries
- Reduced Material Waste
- Recyclability
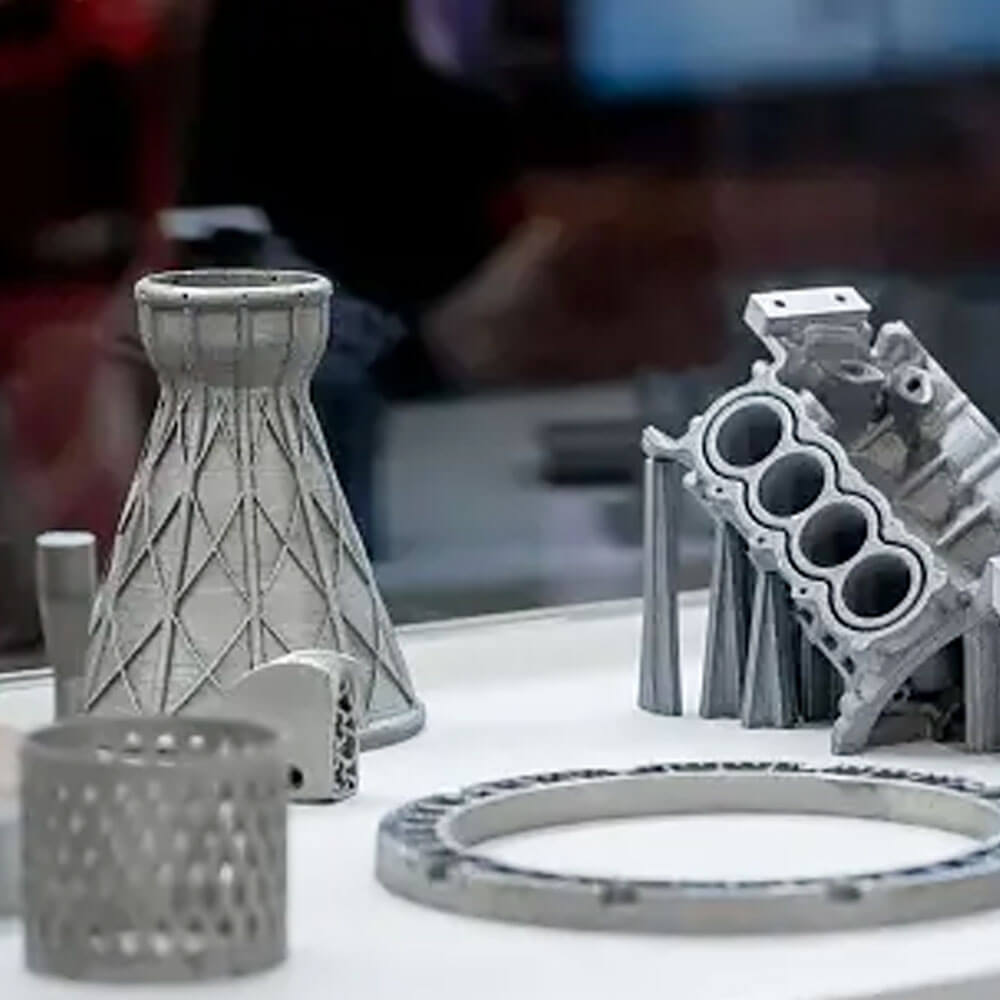