LSR Overmolding Service
Lingshantech stands out as a premier LSR overmolding manufacturer, with over 20 years of experience in delivering cost-effective solutions for precision Liquid Silicone Rubber (LSR) and plastic or metal overmolding components and assemblies.
Rapid Tooling Production
24/7 engineering support
ISO9001:2015
IATF16949
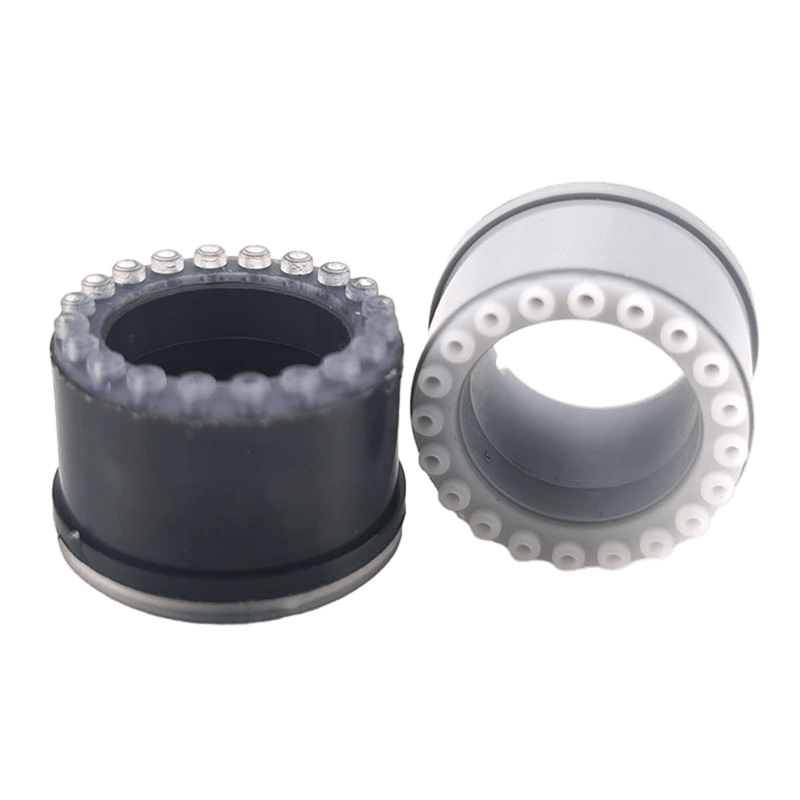
Lingshantech 's Overmolding Service Trusted Manufacturer
Trusted Manufacturer Of LSR Overmolding Products
Lingshantech Silicone Parts is a trusted partner for major OEMs worldwide, specializing in the overmolding process to deliver top-notch parts. With two decades of experience in liquid silicone rubber (LSR) components, advanced production capabilities, and exceptional quality and metrology systems, we are well-equipped to meet your project needs.
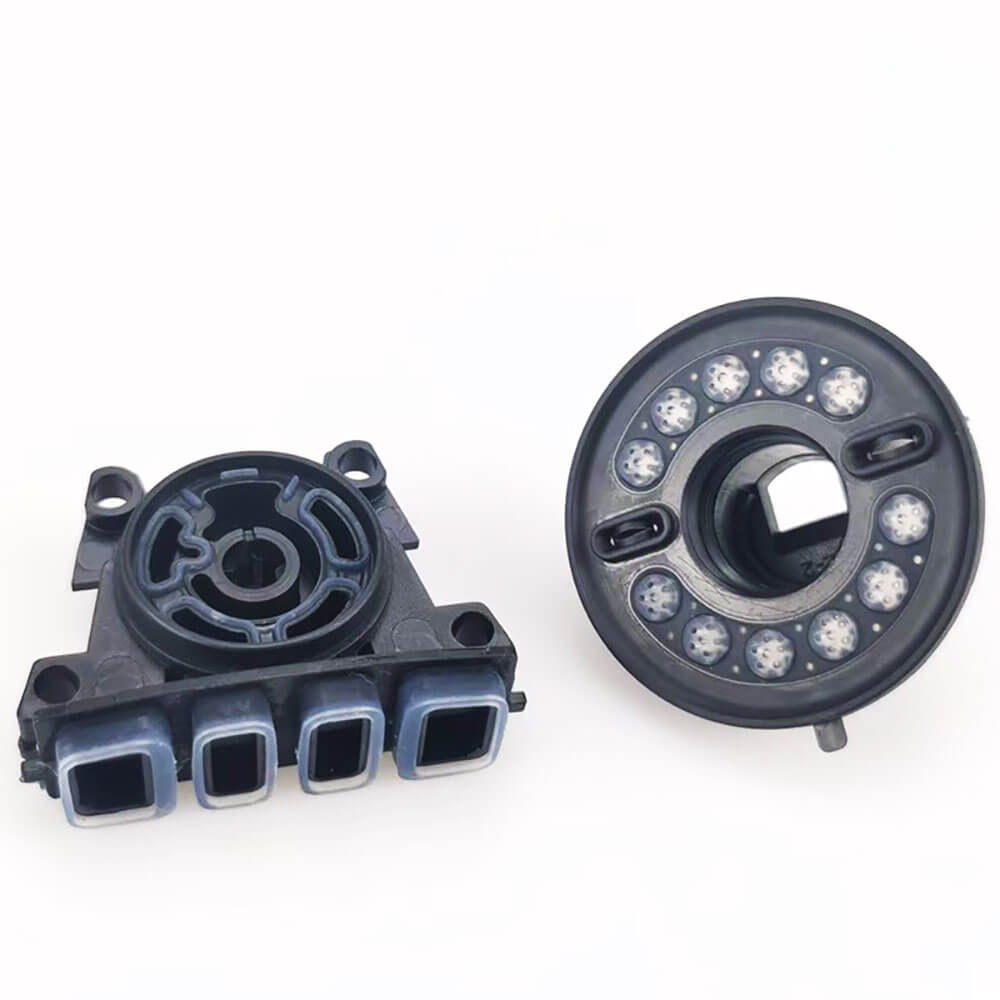
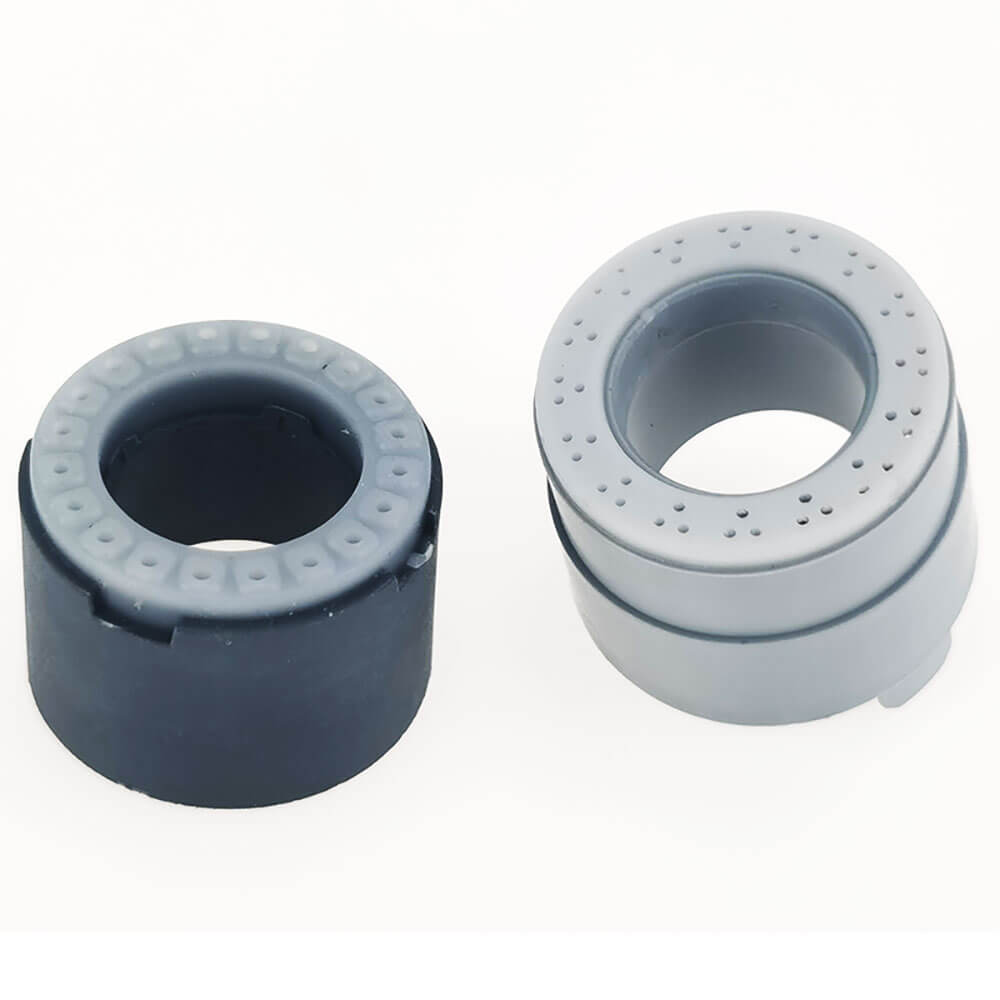
Comprehensive Overmolding Products Solutions
Our comprehensive services encompass the entire Overmolding molding process, offering value-added solutions from design and prototyping to packaging and delivery. Count on us to provide tailored services and outstanding support at every stage of your project.
Why Choose Us?
Extensive Production Capacity
Our advanced manufacturing facility features over 10 sets of LSR injection machines ranging from 60 to 160 tons, providing extensive production capacity and flexibility. We leverage advanced control technology to deliver high-quality LSR products promptly and offer customized solutions to meet specific customer requirements.
Biocompatibility & Performance Properties
With meticulous material selection and testing, we ensure that our LSR materials meet strict medical and healthcare biocompatibility standards for components intended for human contact. Our production process takes place in an advanced 8-grade cleaning room, ensuring a controlled and sterile environment for manufacturing medical-grade LSR components. Adhering to international standards like ISO 9001, our LSR components are safe for medical applications, meeting the stringent requirements of the medical industry.
Multi-material Molding
Lingshantech stands out in multi-material molding, incorporating two-shot, insert, and overmolding techniques. This advantage allows us to combine different LSR materials with other materials in a single mold, enabling diverse and complex product designs. We provide flexibility to meet various performance requirements, customize colors, simplify manufacturing processes, and enhance product quality, positioning us as a leading provider in the LSR injection molding industry.
Precise Control
We employ high-precision injection molding machines and advanced control systems to monitor and adjust key parameters like temperature, pressure, and speed in real-time, ensuring stable and consistent LSR injection. This precise control guarantees consistent product dimensions and quality, meeting the stringent demands for high-quality LSR products from our customers. Whether it's small-batch or large-scale production, we maintain a high level of accuracy throughout the manufacturing process.
Our Unique Points
Die casting is a highly efficient method for producing high-quality prototypes and small-batch parts, making it a versatile choice for various applications. Our team is dedicated to helping you achieve your manufacturing goals by offering expert die casting services
Rapid Prototyping
We possess the ability to swiftly and flexibly generate high-quality prototypes, regardless of material diversity or design modifications. Our manufacturing process upholds a high level of precision and consistency, guaranteeing the provision of outstanding prototypes that serve as robust aids for testing and validating design concepts.
DVT & PVT Testing
We specialize in creating die casting products ideal for market and consumer testing, concept models, and user evaluation during the Design Validation Testing (DVT) and Production Validation Testing (PVT) stages. Our die casting services enable you to swiftly incorporate changes for thorough performance and dimensional testing before market launch.
Pilot & Mass Production
Die cast parts are excellent for custom and first-run production, allowing cost-effective product quality testing before proceeding to full-scale manufacturing. We offer small batch and large-scale production services, accompanied by PPAP (Production Part Approval Process) documentation for quality assurance and validation.
StartMaking Custom Overmolding Parts
Unlock limitless design possibilities and enhanced product performance with our expert custom overmolding solutions – contact us to bring your unique ideas to life!
Available Material for LSR Overmolding
Liquid Silicone Rubber (LSR)
- Liquid Silicone Rubber (LSR)
- Thermoplastic PlasticsABS
PC
PP
PA (Nylon) - Thermoplastic Elastomers (TPE)SEBS
TPU - MetalsAluminum
Steel - Other Elastomeric Materials
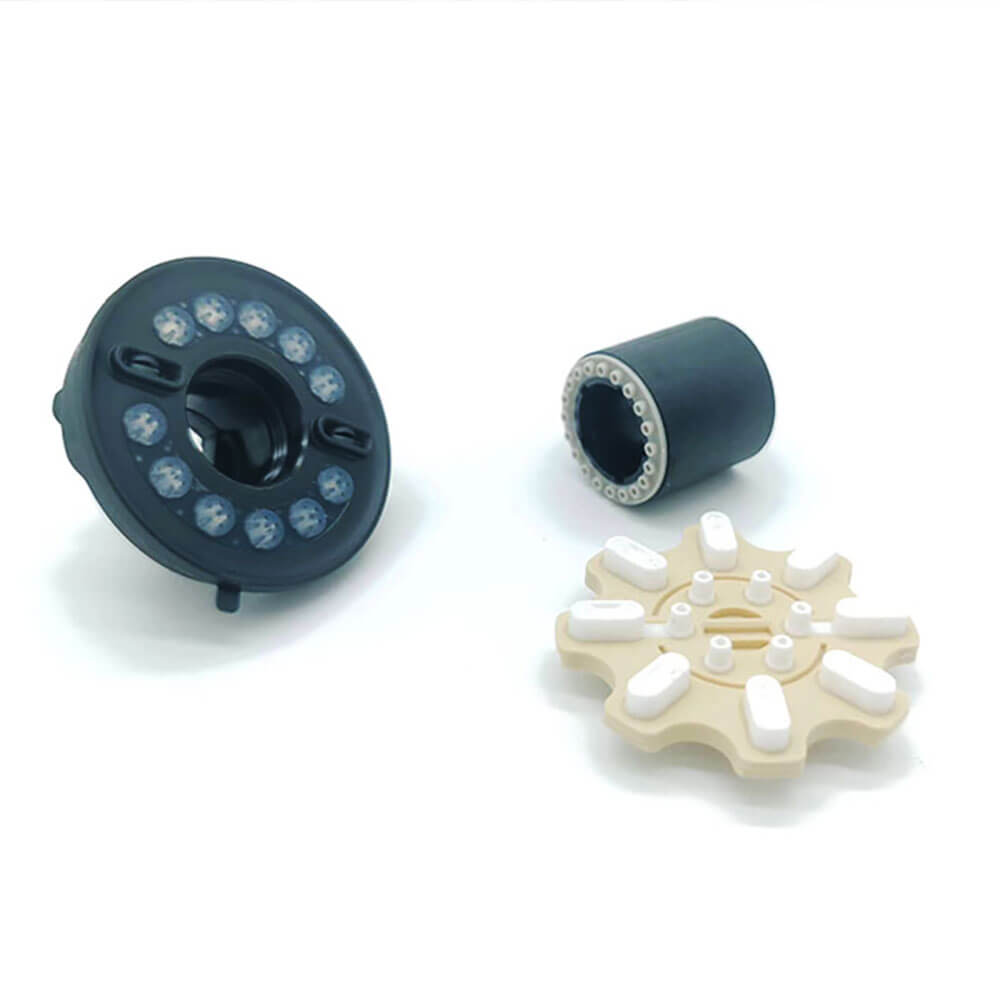
Tolerances
Mold Type | Dimensional Tolerance |
Substrate Molds | ± 0.08 mm, with an included resin tolerance that can be greater but no less than 0.002 in./in. (0.002 mm/mm) |
Thermoplastic Overmolds | Tolerances consistent with substrate molds |
LSR Overmolds | ± 0.025 in./in. (0.025 mm) |
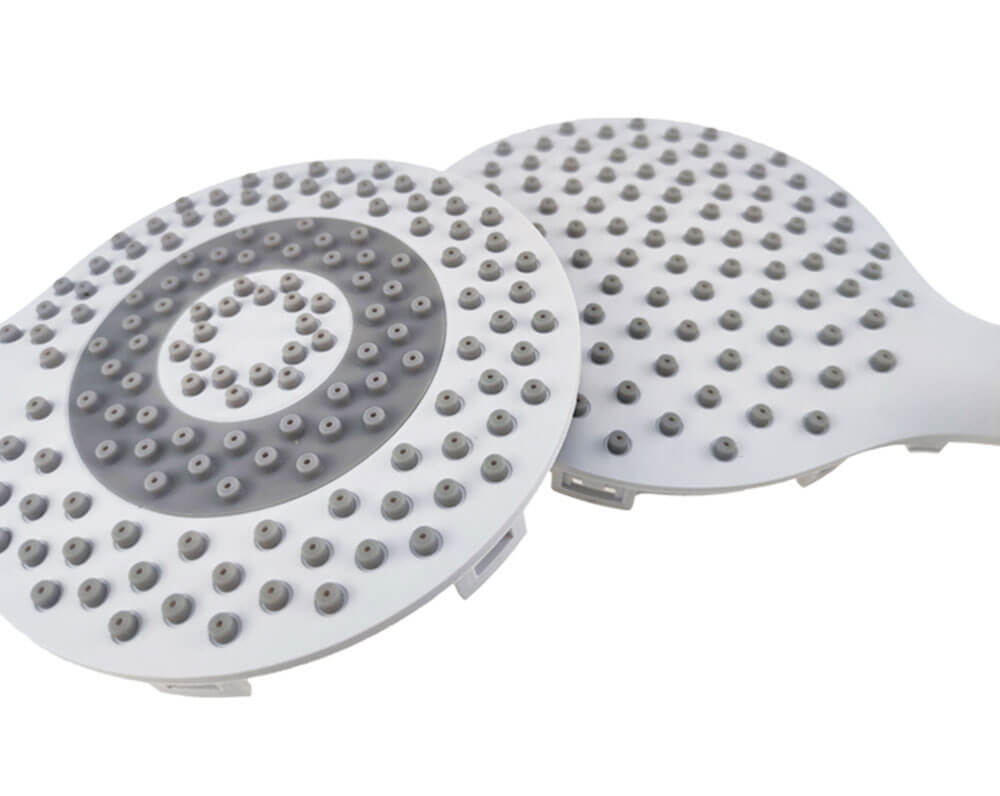
Surface Finish Options for Overmolding
Glossy
- Glossy
- Semi-glossy
- Matte
- Textured
What Is Overmolding?
What Is Overmolding and How It Works?
Overmolding is a manufacturing process where a single part is created by combining two or more materials during the injection molding process. Typically, a rigid plastic or metal component (referred to as the substrate or base part) is molded together with a flexible or elastomeric material (known as the overmold) to create a single integrated component.
Mold Design
A mold is designed to accommodate both the substrate and the overmolding material. It has cavities and runners that allow the molten materials to flow and fill the mold properly.
Bonding and Cooling
When the molten overmolding material comes into contact with the substrate, it bonds to the substrate as it cools and solidifies. This bonding can be mechanical, chemical, or a combination of both, depending on the materials used.
How the Overmolding Works?
Substrate Preparation: The first step is to prepare the substrate, which is typically a rigid or solid part made of a material like plastic, metal, or even another molded component. This substrate serves as the core or base of the final overmolded part.
Injection Molding
The substrate is placed in the mold, and the overmolding material is injected into the mold cavity. Injection molding involves heating the overmolding material to a molten state and then injecting it into the mold under pressure.
Ejection
Once the overmolding has solidified and fully bonded to the substrate, the entire overmolded part is ejected from the mold.
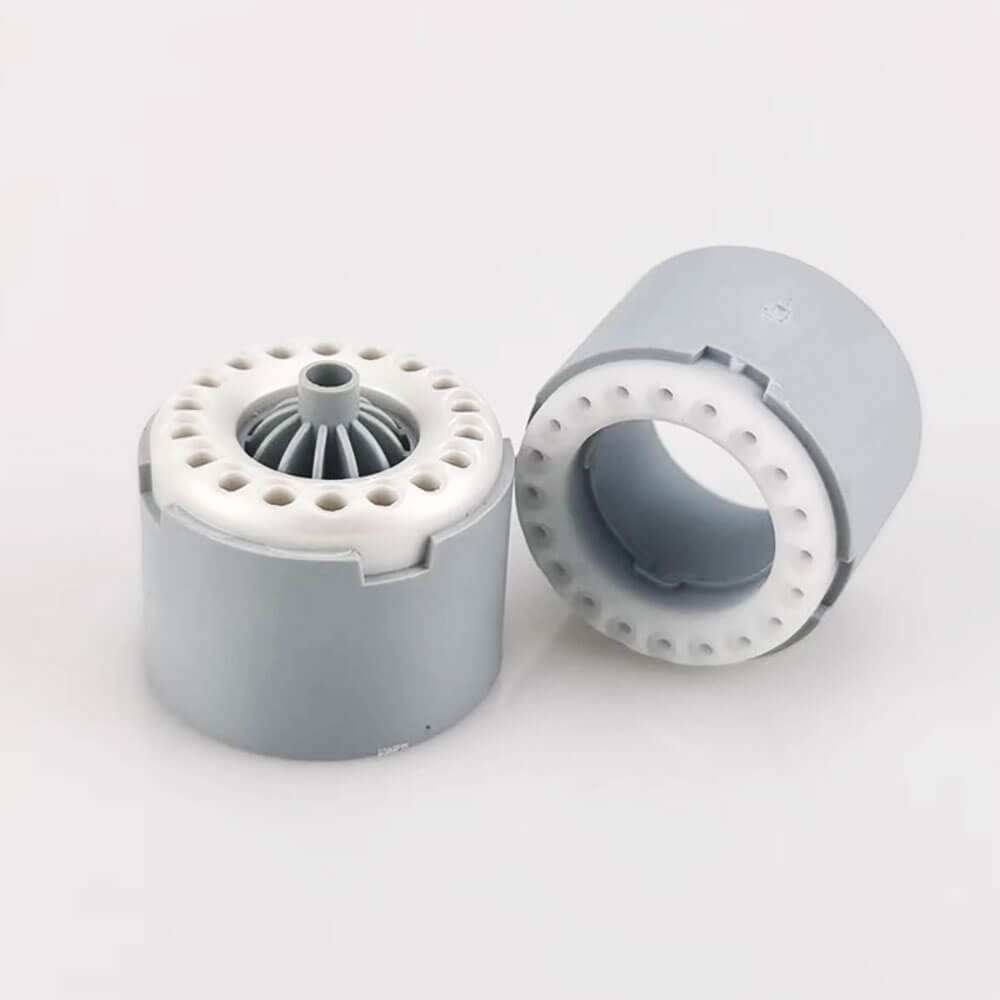
Applications
- Soft-grip handles for hand tools
- Toothbrush grips
- Medical device handles and grips
- Automotive interior components like steering wheels and shift knobs
- Electrical connectors and cables with strain relief
- Sealed and waterproof electronics
- Multi-colored or multi-material parts for consumer goods
- Industrial equipment with ergonomic grips
- Outdoor and sports equipment handles
- Wearable technology for comfortable, durable wearables.