Silicone/LSR Injection Molding
ingshantech boasts over 20 years of expertise in providing cost-effective solutions for precision Silicone Rubber/LSR components and assemblies.
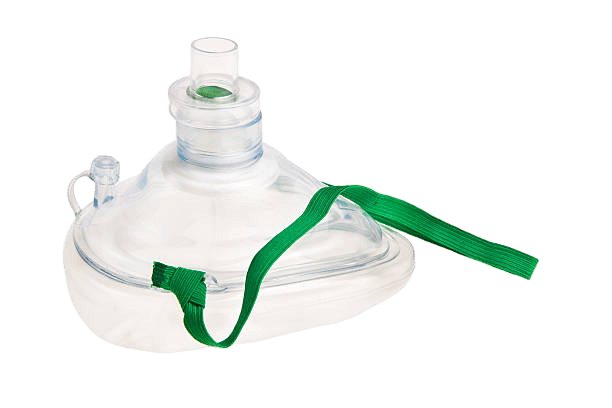
Concept-to-market Silicone Manufacturing
Lingshantech’s silicone divisions offer full-service LSR manufacturing capabilities, including product R&D, prototyping with production representative tooling, LSR tooling manufacturing, class 8 cleanroom production, multi-shot/multi-material molding, and secondary operations for single-source production.
Why Choose Lingshantech for Silicone/LSR Injection Molding
Extensive Production Capacity
Lingshantech offers exciting design and molding opportunities through silicone injection molding. With over 10 sets of LSR injection machines ranging from 60 to 160 tons, our advanced manufacturing facility ensures extensive production capacity and flexibility. Supported by advanced control technology, we deliver high-quality LSR products promptly and provide customized solutions tailored to our customers' specific needs.
Biocompatibility&Performance Properties
We meticulously select and test LSR materials to meet strict medical and healthcare biocompatibility standards for components intended for human contact. Our production process takes place in an advanced 8-grade cleaning room, ensuring a controlled and sterile environment for manufacturing medical-grade LSR components. Adhering to international standards like ISO 9001, our LSR components are safe for medical applications, meeting the stringent requirements of the medical industry.
Multi-material Molding
Lingshantech excels in multi-material molding, incorporating two-shot, insert, and overmolding techniques. With this advantage, we can combine different LSR materials with other materials in a single mold, allowing for diverse and complex product designs. This flexibility enables us to meet various performance requirements, customize colors, simplify manufacturing processes, and enhance product quality, positioning us as a leading provider in the LSR injection molding industry.
Precise Control
By using high-precision injection molding machines and advanced control systems, we can monitor and adjust key parameters like temperature, pressure, and speed in real-time, ensuring stable and consistent LSR injection. This precise control guarantees consistent product dimensions and quality, meeting the stringent demands for high-quality LSR products from our customers. Whether it's small-batch or large-scale production, we maintain a high level of accuracy throughout the manufacturing process.
Our Unique Points
An extensive range of customizable options, seamless collaboration for tailored solutions, and swift manufacturing to capitalize on market opportunities and meet urgent demands
Endless Options
Choose from millions of possible combinations of materials, finishes, tolerances, markings, and certifications for your order.
Seamless Customization
We collaborate closely with you to bring your vision to life. With a wide array of materials, colors, and finishes, your creative ideas take shape with precision and unmatched quality.
Shorter Delivery Times
We can start manufacturing immediately according to your needs, achieving rapid delivery, enabling you to seize the market opportunities and meet urgent customer demands.
Start Silicone / LSR Injection Molding Project Today
Unlock precision and flexibility with our silicone/LSR injection molding expertise. Send us your inquiry today for high-quality, custom silicone parts tailored to your unique requirements.
Materials
Here are some common silicone and Liquid Silicone Rubber (LSR) injection molding materials along with their specific model numbers:
Silicone Rubber Elastomers:
General-Purpose Silicone: such as, Silastic® RTV-2 Silicone Rubber.
High Hardness Silicone: such as, Dow Corning® Silastic® E RTV-2 Silicone Rubber.
Medical-Grade Silicone:
NuSil® MED-4850 Silicone Rubber.
Dow Corning® QP1 Silicone Rubber.
High-Temperature Silicone:
Shin-Etsu KEG-2000 Silicone Rubber.
Wacker Elastosil® LR 3003/50 Silicone Rubber.
Conductive Silicone:
Dow Corning® Silastic® DC 595 Silicone Rubber.
Wacker Elastosil® LR 3003/60 CN Silicone Rubber.
Flame-Retardant Silicone:
Dow Corning® Silastic® FR 7 Silicone Rubber.
Shin-Etsu KE-1300T Silicone Rubber.
Food-Grade Silicone:
Dow Corning® Silastic® FDA Silicone Rubber.
NuSil® MED-6645 Silicone Rubber.
Liquid Silicone Rubber (LSR):
Wacker Elastosil® LR 3003/60 Silicone Rubber.
Dow Corning® Silastic® LSR 5-9970 Silicone Rubber.
Self-Lubricating Silicone:
Dow Corning® Silastic® XLS Silicone Rubber.
Shin-Etsu KEG-300 Silicone Rubber.
Transparent Silicone:
NuSil® CF-40 Silicone Rubber.
Wacker Elastosil® LR 3003/70 Silicone Rubber.
Conductive Silicone:
Dow Corning® Silastic® E RTV-2 CN Silicone Rubber.
Shin-Etsu KEG-300-4 CN Silicone Rubber.
Tolerances
Part to Part Repeatability | +/- 0.1 mm +/- 0.0039 in. |
Mold Cavity Tolerances | +/- 0.05 mm +/- 0.002 in. |
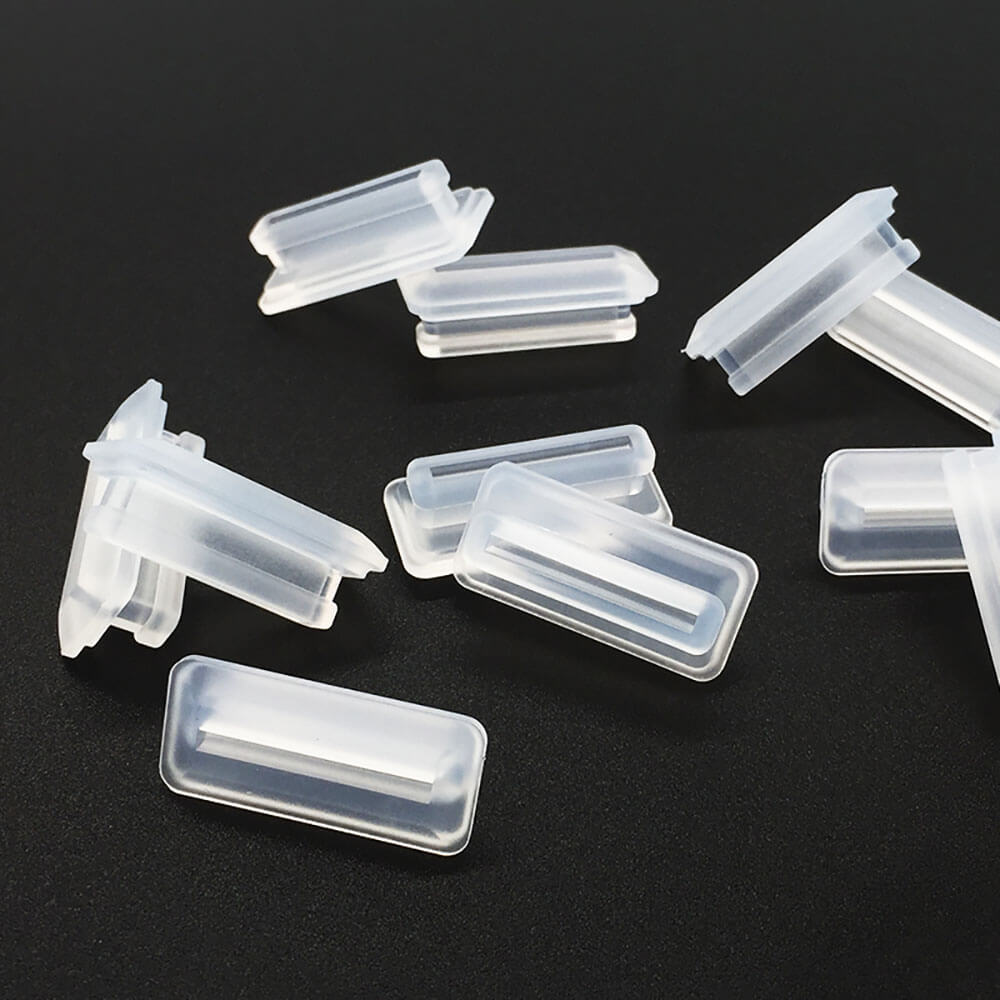
Surface Finish Options for Silicone/LSR Injection Molding
- Natural Surface
- Polishing
- Silicone Coating
- Screen Printing
- Color Additions
- UV Protection
What Is Silicone/LSR Injection Molding?
Silicone/LSR (Liquid Silicone Rubber) injection molding is a manufacturing process used to produce parts and components from silicone or LSR materials. It is a highly versatile and efficient method for creating complex, precise, and durable silicone products. The process involves injecting liquid silicone rubber into a mold cavity, where it is cured to form the desired shape.
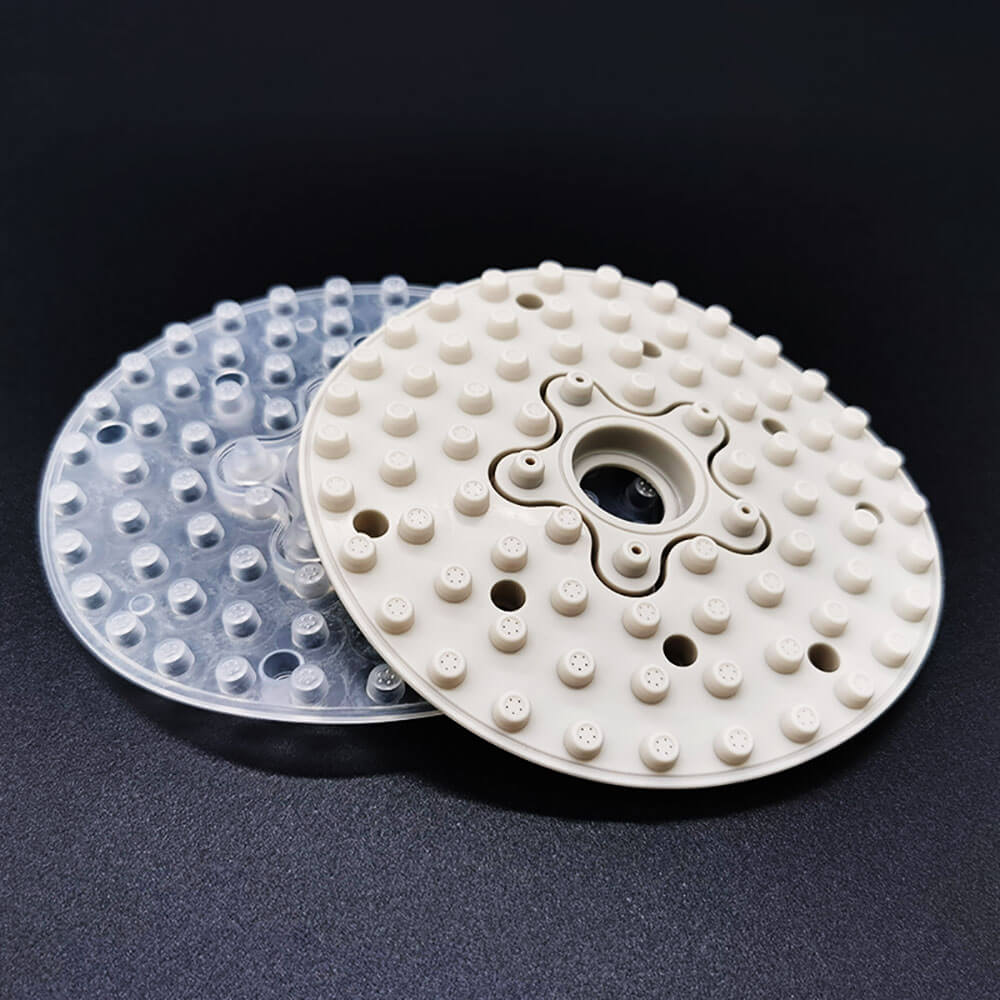
Key Features and Steps of Silicone/LSR Injection Molding Include:
- Material Preparation
- Injection
- Curing
- Demolding
- Post-processing (if necessary)
Applications of Silicone/LSR Injection Molding
- Medical: Silicone/LSR molding for medical equipment like seals, catheters, and high-temperature-resistant components due to biocompatibility and chemical resistance.
- Automotive: Used in vehicles for seals, mud flaps, thermal pads, connectors, and exhaust parts, thanks to high-temperature and aging resistance.
- Electronics: Ideal for sealing, insulating, and waterproofing electronic devices such as smartphone cases, connectors, and gaskets.
- Consumer Goods: Employed in consumer products like kitchen utensils, baby bottle nipples, watch straps, and swim goggles due to durability and water resistance.
- Industrial: Used in industrial settings for sealing rings, gaskets, vibration dampers, valve components, and more.
- Food and Beverage: Compliant with food safety standards for food-grade seals, molds, oven gaskets, etc.
- Aerospace: Used in aerospace for high-temperature seals, vibration dampers, spacecraft seals, and fuel system components.
- Construction: Applied in building and construction for seals, insulation gaskets, and waterproof coating materials.
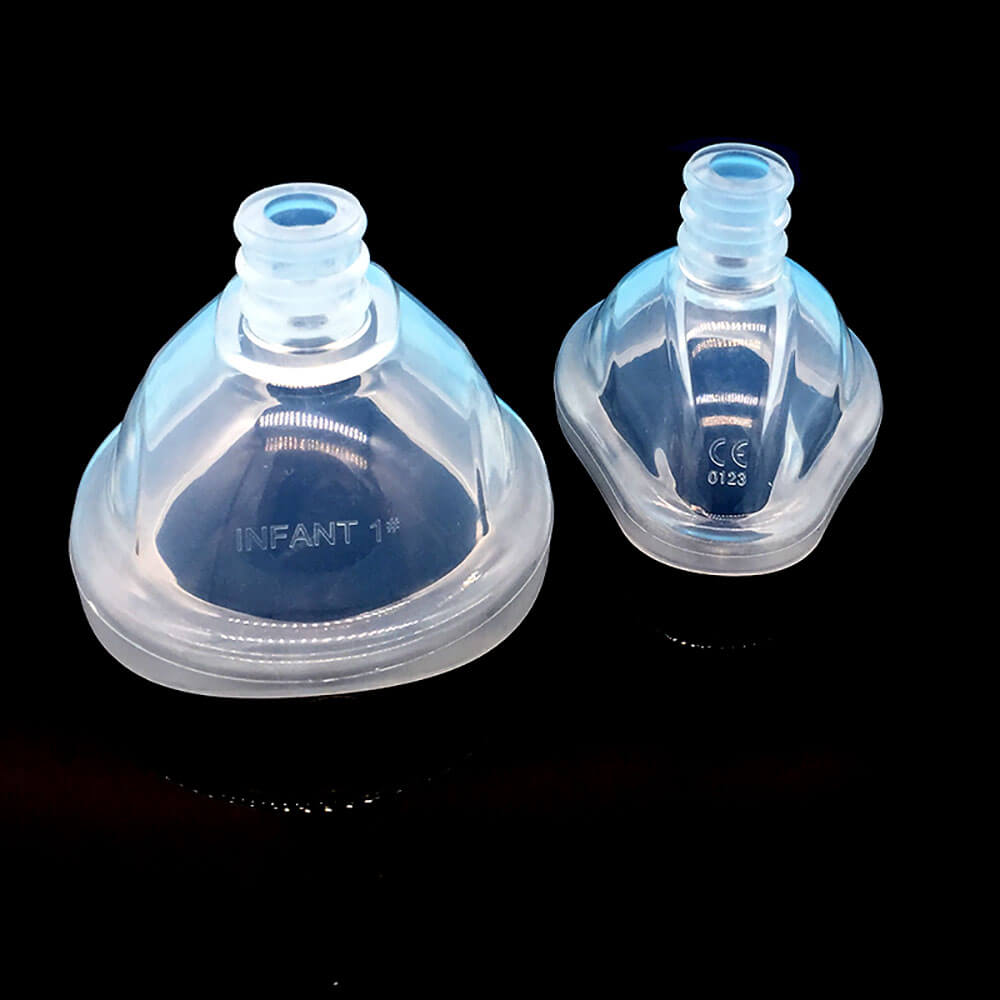